Who we are
The Insurance Institute for Highway Safety (IIHS) is an independent, nonprofit scientific and educational organization dedicated to reducing deaths, injuries and property damage from motor vehicle crashes through research and evaluation and through education of consumers, policymakers and safety professionals.
The Highway Loss Data Institute (HLDI) shares and supports this mission through scientific studies of insurance data representing the human and economic losses resulting from the ownership and operation of different types of vehicles and by publishing insurance loss results by vehicle make and model.
Media queries? Please see our Press room.
Insurance Institute for Highway Safety
IIHS was founded in 1959 by three major insurance associations representing 80% of the U.S. auto insurance market. At first, the Institute's purpose was to support highway safety efforts by others. A decade later, IIHS was reinvented as an independent research organization. William Haddon Jr., M.D., who served as the nation's first federal highway safety chief, oversaw this transition after becoming president of IIHS in 1969. By then, he already was leading the transformation of the highway safety field from one focused solely on crash prevention to one using a modern, scientific approach to identify a full range of options for reducing crash losses. In particular:
- Human factors research addresses problems associated with teenage drivers, alcohol-impaired driving, truck driver fatigue and seat belt use, to name a few.
- Vehicle research focuses on both crash avoidance and crashworthiness. Crash tests are central to crashworthiness research, and IIHS testing expanded with the opening of the Vehicle Research Center (VRC).
- Research about the physical environment includes, for example, assessment of roadway designs to reduce run-off-the-road crashes and eliminate roadside hazards.
This scientific approach has been remarkably successful. The number of people killed on roads in the United States, while still far too high, has fallen since 1979, even as the population and the number of miles driven have climbed. Much of this improvement is a result of safer vehicles.
At the same time, IIHS recognizes that vehicle design isn't the whole story and continues to look for ways to improve driver behavior and roadway design. For example, our work has led more states to adopt primary seat belt laws and graduated licensing requirements and has encouraged communities to build roundabouts and use automated enforcement, including red light and speed cameras.
Vehicle Research Center
In 1992, IIHS opened the VRC. Tucked in the foothills of central Virginia, this state-of-the-art facility is where we perform the crash tests and other evaluations that form the basis of our widely consulted vehicle ratings.
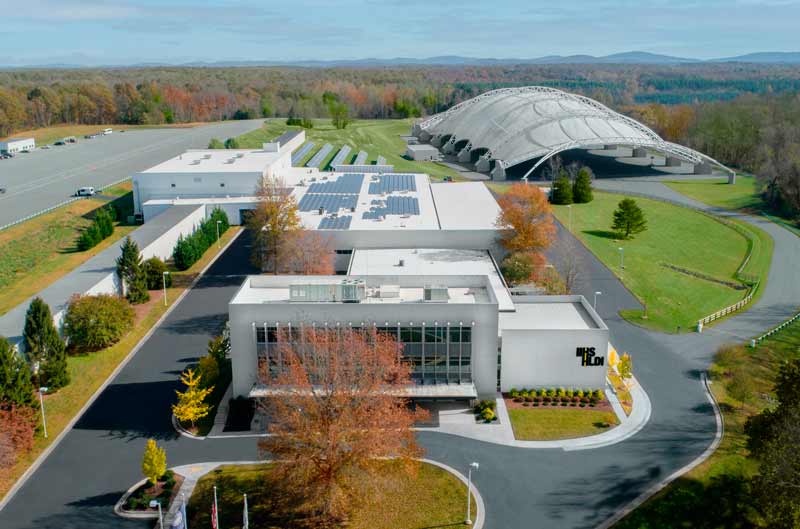
VRC tests help consumers make informed decisions. Vehicles are rated for safety based on performance in several tests, and the best performers carry the Top Safety Pick+ or Top Safety Pick designation. IIHS tests have encouraged automakers to produce safer vehicles, which is the ultimate goal. Knowing that consumers consult the ratings before buying, manufacturers design cars and trucks with these tests in mind.
We began issuing crash test ratings in 1995, beginning with a moderate overlap front test. At first, about half of vehicles earned marginal or poor ratings, and more were rated poor than good. The ratings quickly improved, and virtually all vehicles have earned good ratings in that original test since the 2013 model year.
That pattern has been repeated with other types of frontal crash tests, as well as side crash tests and head restraint and roof strength evaluations. As automakers have met these challenges, we have raised the bar, introducing tougher tests.
In 2013, IIHS testing expanded beyond crash protection to crash avoidance. We began by rating vehicles for front crash prevention. At the time, technology that could detect an impending frontal collision and initiate automatic emergency braking was just beginning to spread through the marketplace, and our ratings helped speed its adoption.
An expansion of the VRC completed in 2015 enhanced our crash avoidance testing capabilities. We added nighttime tests of headlight performance on our enlarged track and began testing front crash prevention systems for their ability to avoid pedestrians in addition to other vehicles. We run pedestrian tests both during daylight hours and at night, and our covered track allows this work to continue rain or shine.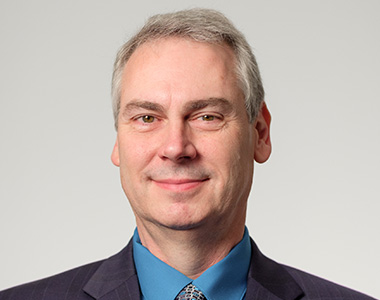
David Harkey
is the current president of the Insurance Institute for Highway Safety and the affiliated Highway Loss Data Institute. He took the helm of the Institutes in 2018 after spending 11 years as director of the University of North Carolina Highway Safety Research Center.
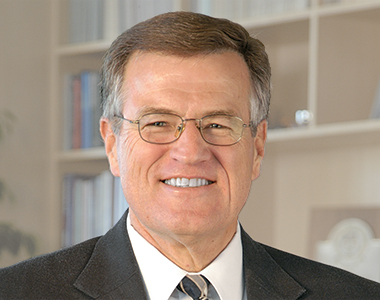
Adrian Lund
served as president of IIHS and HLDI from 2006 to 2017. He joined IIHS in 1981 as a behavioral scientist.
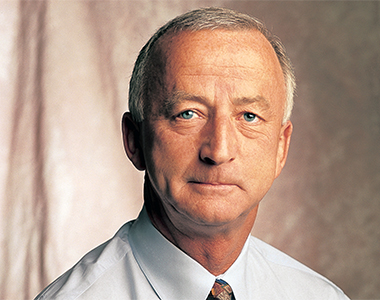
Brian O'Neill
served as president of IIHS and HLDI from 1985 until January 2006. He joined the IIHS in 1969.
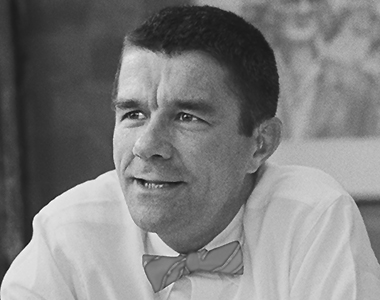
William Haddon Jr., M.D.
became IIHS president in 1969 and served until his death in 1985. He was the first federal highway safety chief.
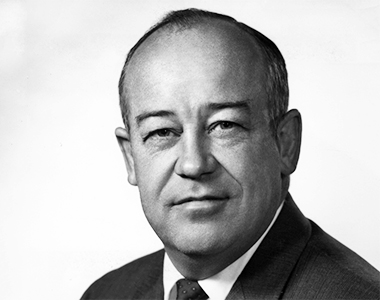
Russell Ira Brown
was the first IIHS president, serving from 1959 until 1967.
Highway Loss Data Institute
HLDI is a nonprofit research organization that publishes insurance loss statistics on most car, SUV, pickup truck and motorcycle models on U.S. and Canadian roads. Founded in 1972, HLDI regularly analyzes losses under six insurance coverages — collision, property damage liability, personal injury protection, medical payment, bodily injury liability and comprehensive (including theft). HLDI collects data from companies representing over 85% of the U.S. market for private passenger vehicle insurance. Its database is the largest repository of such information in the world.
Information from HLDI helps car buyers make informed choices. Insurance losses vary widely among vehicles — even among those that are similar in size and type. Some competing models may have much lower occupant injury experience than others and may be less expensive to insure. HLDI publishes insurance losses by make and model. Through its ability to analyze and make such information useful, HLDI has become the nation's principal source of public information about insurance losses for automobiles and other passenger vehicles.
HLDI also analyzes the effects of various safety and crash avoidance features, such as electronic stability control (ESC), forward collision warning and adaptive headlights.
One of HLDI's first-ever findings was that collision coverage losses weren't higher for larger car models, though most people had presumed they were. It found that smaller cars had higher collision coverage losses, despite a widespread belief that small cars offered greater maneuverability to avoid crashes.
HLDI research revealed that vehicles equipped with ESC clearly show lower overall collision losses, with reductions ranging from 15% to 17%. With this knowledge, along with data from IIHS research on ESC, more and more manufacturers began including the feature on their vehicles. The federal government now requires the technology on all new passenger vehicles.
As manufacturers introduce new crash avoidance features, HLDI is examining their real-world effectiveness.
HLDI's work has been modeled around the world. Countries such as Canada, Australia and South Korea have formed associations that compile and publish similar information.
Milestones
Much has changed on the nation's roads since the Insurance Institute for Highway Safety (IIHS) was founded more than half a century ago — and many of those changes came about as a result of IIHS work. Here are some key dates from our history.
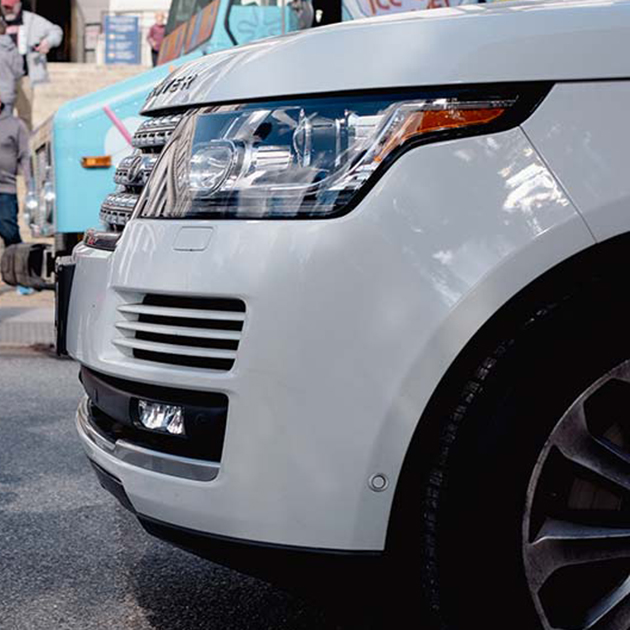
Amid rising pedestrian deaths, IIHS researchers find that vehicles with tall or blunt front ends are more likely to kill pedestrians when they strike them than vehicles with short, sloping front ends.
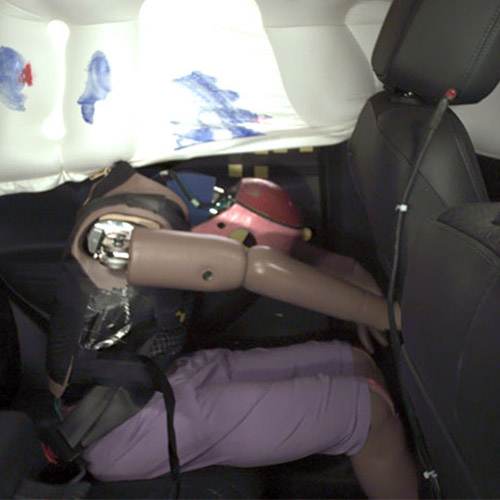
IIHS updates the long-running moderate overlap front test by adding a second dummy in back, challenging automakers to improve rear-seat protection.
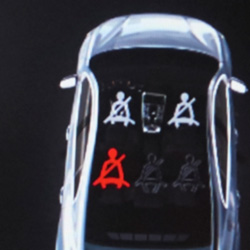
IIHS begins rating seat belt reminders to encourage loud, persistent alerts that persuade people to buckle up on every trip.
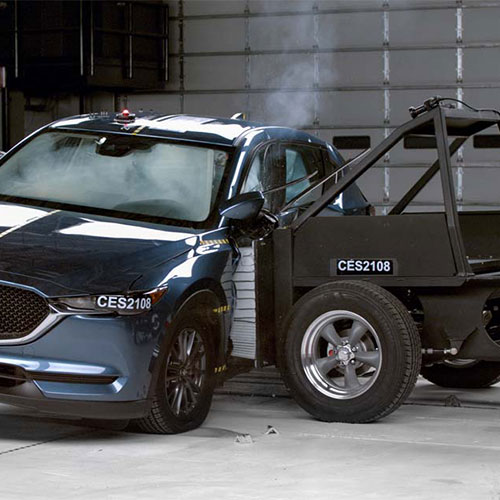
IIHS rolls out an updated side crash test. The new test, conducted at a higher speed with a heavier striking barrier, was developed to encourage further improvements now that the vast majority of new vehicles earn a good rating in the original side test.
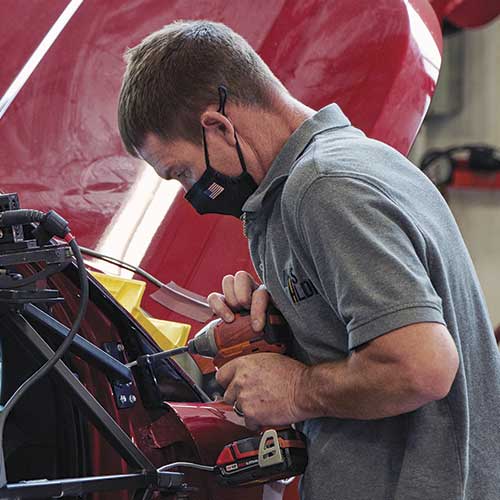
VRC staff adapts to the constraints of the COVID-19 pandemic, resuming testing at the facility with alternating skeleton crews following a three-month closure.
IIHS issues detailed, research-based safety guidelines for the design of partially automated driving systems. The systems should share control with the driver and have built-in limits and escalating attention reminders to bring the driver's focus back if it wanders.
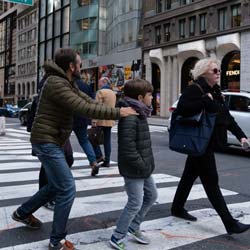
IIHS launches ratings of automatic emergency braking systems that recognize and stop for pedestrians.
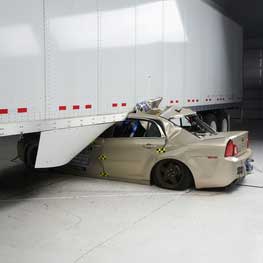
An IIHS testing program prompts major improvements in rear underride guards on semitrailers, as the last of the eight largest North American trailer manufacturers earns the Toughguard award. The award is given for rear guards capable of preventing cars from going under trailers in a range of crash scenarios.
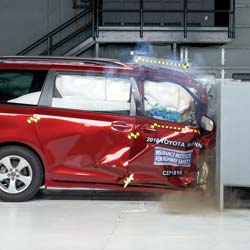
After several years of steady improvements in small overlap front protection on the driver side, IIHS launches the passenger-side small overlap front test to encourage manufacturers to optimize crashworthiness on both sides of the vehicle.
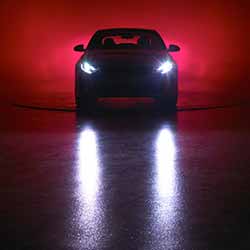
IIHS launches headlight ratings, filling a void in information about this basic equipment.
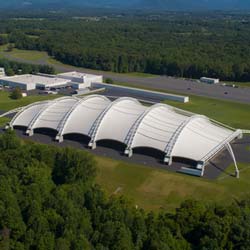
IIHS completes a $30 million expansion of its Vehicle Research Center to enable it to evaluate crash avoidance technologies year-round.
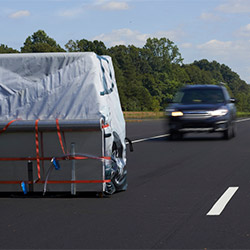
IIHS and the National Highway Traffic Safety Administration announce a voluntary commitment by 10 automakers to equip all new vehicles with a standard front crash prevention system with automatic braking. More manufacturers sign on in subsequent months, with more than 99% of the U.S. vehicle market ultimately represented.
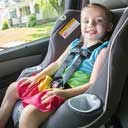
IIHS issues its first LATCH ratings, providing information on how easy or hard it is to install child restraints in more than 100 vehicles.
After research shows many teenagers aren't driving the safest vehicles, IIHS issues its first recommendations on used vehicles for young drivers.
IIHS launches its first test program of an advanced crash avoidance technology, rating vehicles for front crash prevention.
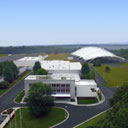
IIHS embarks on a major expansion of the VRC to accommodate more research on advanced crash avoidance systems. The work includes an expansion of the existing test track and the construction of a covered track to allow for testing in all kinds of weather.
IIHS introduces a small overlap frontal test to drive further improvements in crash protection. Most vehicles initially earn poor or marginal ratings.
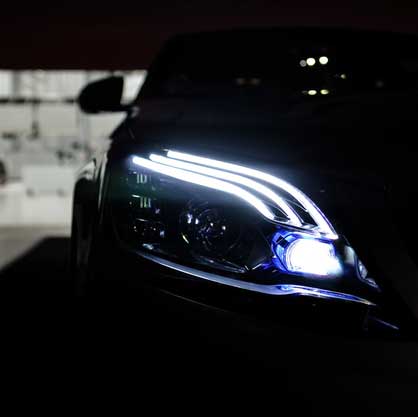
HLDI analysis of insurance claims data shows that forward collision warning and adaptive headlights are reducing crashes.
In the first real-world study of advanced crash avoidance systems, HLDI shows that Volvo's City Safety, a forward collision avoidance system, prevents crashes.
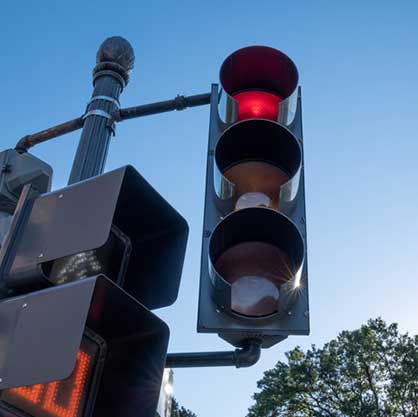
An IIHS study of red light cameras in use in 14 large cities finds the devices reduce the fatal red light running crash rate by nearly a quarter.
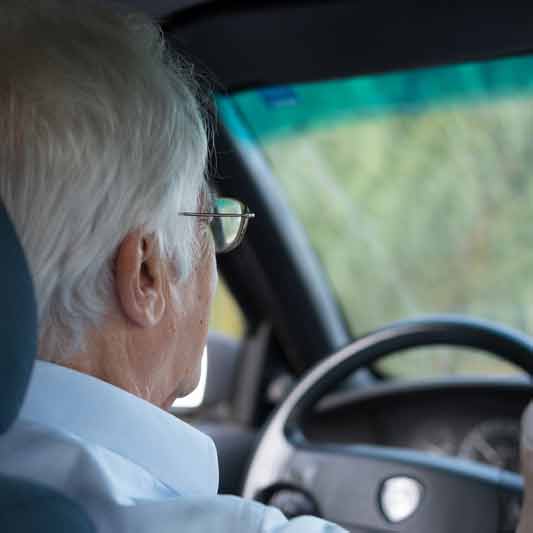
Contrary to expectations, IIHS study finds that older drivers aren't dying more often in crashes, even though they're holding onto their licenses longer.
IIHS crash tests demonstrate the safety risks of allowing low-speed vehicles, which are exempt from federal safety standards for passenger vehicles, on public roads.
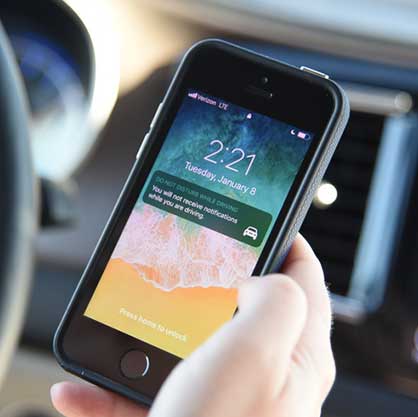
HLDI examines the effectiveness of state bans on handheld cellphones and texting, determining that neither restriction reduces crashes.
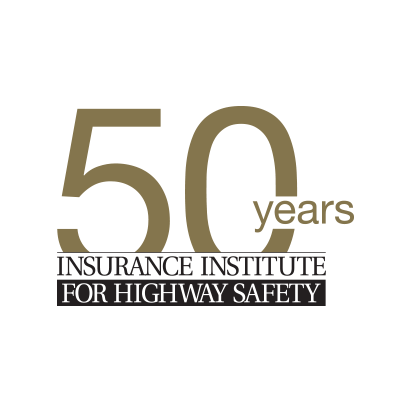
In honor of its 50th anniversary, IIHS conducts a crash test that shows just how much vehicle safety has improved. The test is a 40 mph moderate overlap frontal crash involving two Chevrolets, a 1959 Bel Air and a 2009 Malibu. The Malibu's structure holds up well, while the Bel Air crumples around the driver dummy.
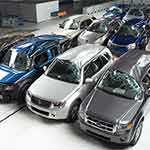
IIHS launches roof strength ratings to help consumers choose vehicles that will protect them in rollovers. A good roof strength rating becomes a requirement for Top Safety Pick.
IIHS is first to compare booster seats and rate their potential effectiveness based on how well they improve the fit of adult lap and shoulder belts for children too old for child restraints but too young for belts alone.
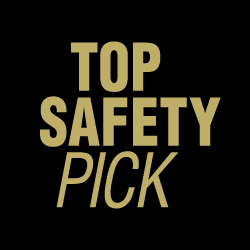
The first Top Safety Pick awards recognize vehicles with top ratings in IIHS front, side and rear tests.
IIHS finds huge benefits of electronic stability control in reducing serious crashes, accelerating introduction of this feature ahead of federal requirements.
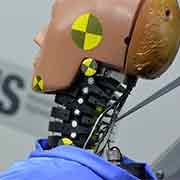
A dynamic test simulating a rear impact is added to the Institute's head restraint evaluations. The test uses a new kind of dummy specifically designed to measure neck injury potential in rear crashes.
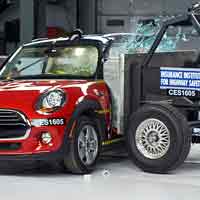
IIHS launches crash tests to rate crashworthiness in side impacts. Automakers respond by improving vehicle designs to provide better protection in side impacts.
Years of IIHS research on teen drivers pay off when the nation's first three-stage graduated licensing law goes into effect in Florida.
IIHS rates head restraints for their potential to protect people's necks in rear-end crashes. Automakers respond with designs that reduce neck injury risk.
IIHS launches offset crash testing to rate frontal crashworthiness. Automakers respond by improving vehicle designs to provide better occupant protection in frontal crashes.
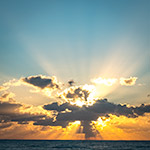
IIHS reveals that daylight saving time reduces crash deaths, a finding that contributes to the subsequent designation of more weeks clock-forward.
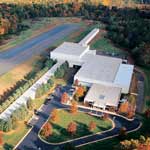
IIHS opens the Vehicle Research Center (VRC) in Ruckersville, Virginia.
Two 1989 Chrysler LeBarons collide head-on in rural Virginia. Both drivers walk away with minor injuries. The crash, believed to be the first of its kind involving two airbag-equipped vehicles, vindicates IIHS and other safety advocates who lobbied for decades for an airbag requirement, which had just been enacted.
IIHS publishes the first consumer information that compares death rates among drivers by vehicle make and model.
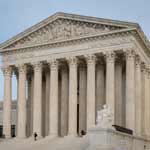
The Supreme Court rules in favor of insurers' efforts to get airbags in cars.
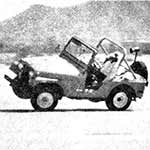
IIHS appears on primetime television in "60 Minutes" segment on Jeep rollover dangers.
.jpg)
IIHS is first to document the hazards to pedestrians of allowing motorists to turn right at red lights. This leads policymakers in New York City and elsewhere to resist or limit the practice of allowing right turns on red.
IIHS tests demonstrate the tendency of the Jeep CJ to roll over, prompting the government to require rollover warnings on some vehicles.
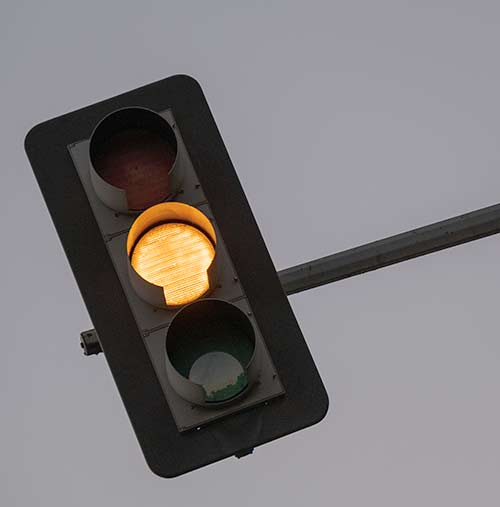
IIHS research on signal timing leads traffic engineers to lengthen yellow light intervals.
IIHS crash tests demonstrate airbag effectiveness in frontal crashes. Highlights are shown before a U.S. congressional committee.
IIHS develops the injury severity score to help medical personnel assess the threat to life of injuries to multiple body parts.
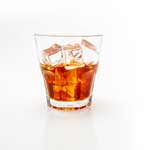
IIHS evaluates the consequences of lowering the legal minimum age for purchasing alcohol. Findings provide the scientific basis for enacting 21 minimum age laws in all states.
IIHS crash tests demonstrate that car fuel system designs allow ruptures, gas leaks and fires in rear crashes. This leads to new federal rules to reduce leaks.
The Highway Loss Data Institute (HLDI) is organized as an affiliate of IIHS to collect, analyze and publish insurance loss information on most car, SUV, pickup truck and motorcycle models on U.S. roads.
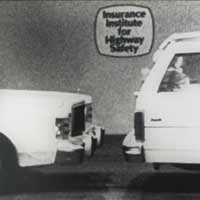
IIHS launches bumper tests, which lead to the first federal bumper standard.
IIHS becomes a scientific research and communications organization after the Board of Governors votes to change its mission.
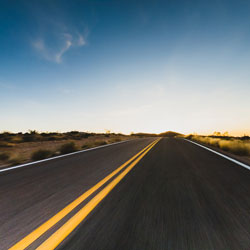
Three insurance industry groups representing more than 500 auto insurers establish IIHS to funnel support to academic and other organizations in the field of highway safety.
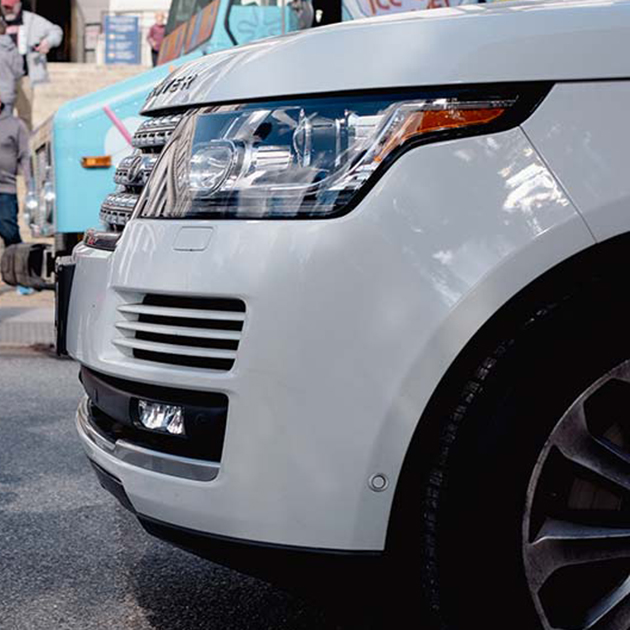
Amid rising pedestrian deaths, IIHS researchers find that vehicles with tall or blunt front ends are more likely to kill pedestrians when they strike them than vehicles with short, sloping front ends.
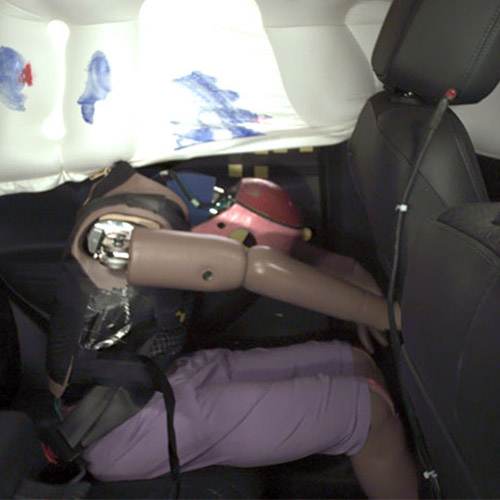
IIHS updates the long-running moderate overlap front test by adding a second dummy in back, challenging automakers to improve rear-seat protection.
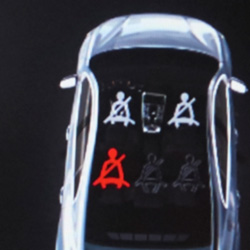
IIHS begins rating seat belt reminders to encourage loud, persistent alerts that persuade people to buckle up on every trip.
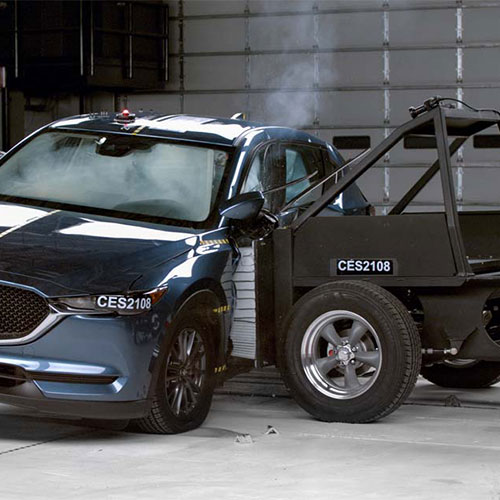
IIHS rolls out an updated side crash test. The new test, conducted at a higher speed with a heavier striking barrier, was developed to encourage further improvements now that the vast majority of new vehicles earn a good rating in the original side test.
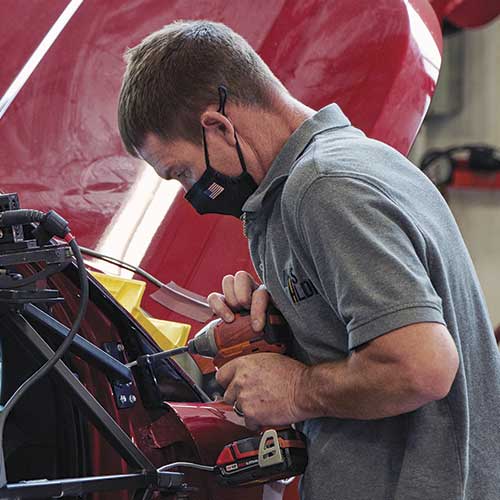
VRC staff adapts to the constraints of the COVID-19 pandemic, resuming testing at the facility with alternating skeleton crews following a three-month closure.
IIHS issues detailed, research-based safety guidelines for the design of partially automated driving systems. The systems should share control with the driver and have built-in limits and escalating attention reminders to bring the driver's focus back if it wanders.
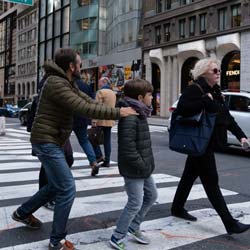
IIHS launches ratings of automatic emergency braking systems that recognize and stop for pedestrians..
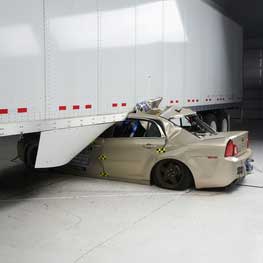
An IIHS testing program prompts major improvements in rear underride guards on semitrailers, as the last of the eight largest North American trailer manufacturers earns the Toughguard award. The award is given for rear guards capable of preventing cars from going under trailers in a range of crash scenarios.
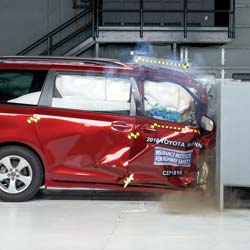
After several years of steady improvements in small overlap front protection on the driver side, IIHS launches the passenger-side small overlap front test to encourage manufacturers to optimize crashworthiness on both sides of the vehicle.
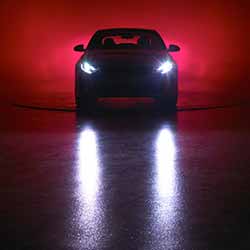
IIHS launches headlight ratings, filling a void in information about this basic equipment.
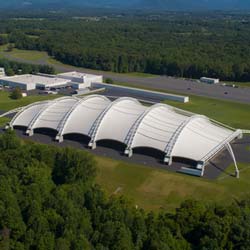
IIHS completes a $30 million expansion of its Vehicle Research Center to enable it to evaluate crash avoidance technologies year-round.
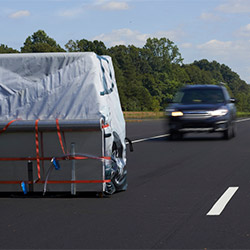
IIHS and the National Highway Traffic Safety Administration announce a voluntary commitment by 10 automakers to equip all new vehicles with a standard front crash prevention system with automatic braking. More manufacturers sign on in subsequent months, with more than 99 percent of the U.S. vehicle market ultimately represented.
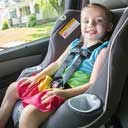
IIHS issues its first LATCH ratings, providing information on how easy or hard it is to install child restraints in more than 100 vehicles.
After research shows many teenagers aren't driving the safest vehicles, IIHS issues its first recommendations on used vehicles for young drivers.
IIHS launches its first test program of an advanced crash avoidance technology, rating vehicles for front crash prevention.
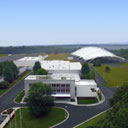
IIHS embarks on a major expansion of the VRC to accommodate more research on advanced crash avoidance systems. The work includes an expansion of the existing test track and the construction of a covered track to allow for testing in all kinds of weather.
IIHS introduces a small overlap frontal test to drive further improvements in crash protection. Most vehicles initially earn poor or marginal ratings.
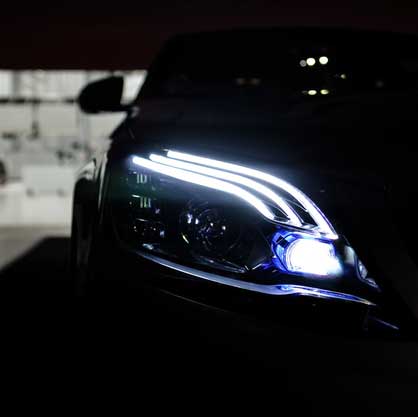
HLDI analysis of insurance claims data shows that forward collision warning and adaptive headlights are reducing crashes.
In the first real-world study of advanced crash avoidance systems, HLDI shows that Volvo's City Safety, a forward collision avoidance system, prevents crashes.
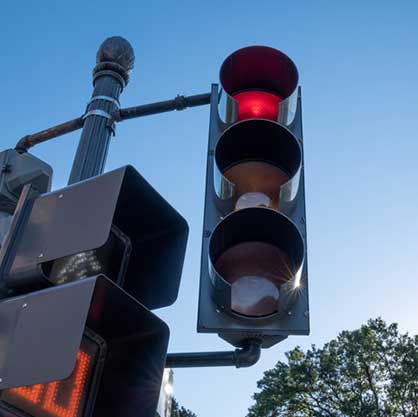
An IIHS study of red light cameras in use in 14 large cities finds the devices reduce the fatal red light running crash rate by nearly a quarter.
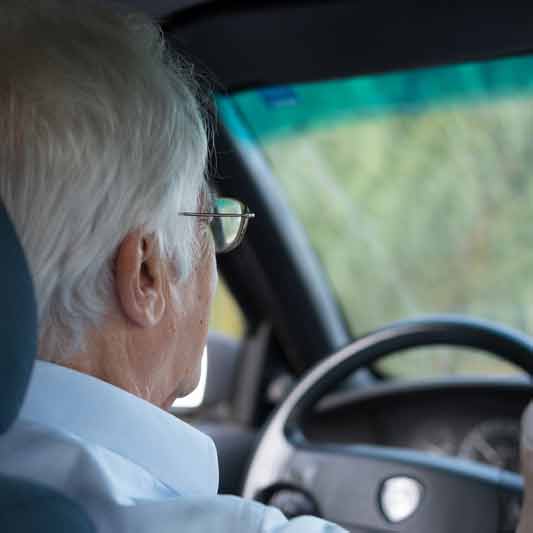
Contrary to expectations, IIHS study finds that older drivers aren't dying more often in crashes, even though they're holding onto their licenses longer.
IIHS crash tests demonstrate the safety risks of allowing low-speed vehicles, which are exempt from federal safety standards for passenger vehicles, on public roads.
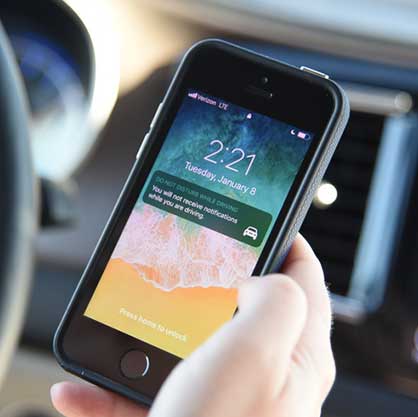
HLDI examines the effectiveness of state bans on handheld cellphones and texting, determining that neither restriction reduces crashes.
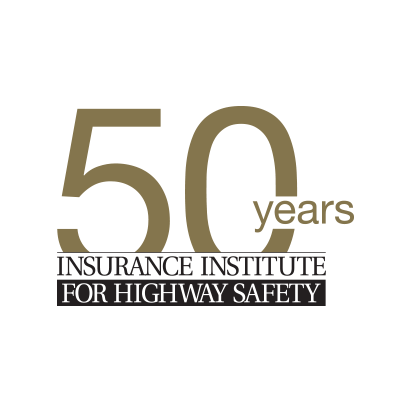
In honor of its 50th anniversary, IIHS conducts a crash test that shows just how much vehicle safety has improved. The test is a 40 mph moderate overlap frontal crash involving two Chevrolets, a 1959 Bel Air and a 2009 Malibu. The Malibu's structure holds up well, while the Bel Air crumples around the driver dummy.
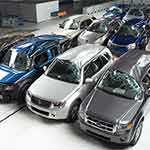
IIHS launches roof strength ratings to help consumers choose vehicles that will protect them in rollovers. A good roof strength rating becomes a requirement for Top Safety Pick.
IIHS is first to compare booster seats and rate their potential effectiveness based on how well they improve the fit of adult lap and shoulder belts for children too old for child restraints but too young for belts alone.
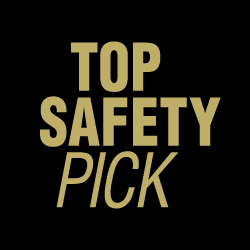
The first Top Safety Pick awards recognize vehicles with top ratings in IIHS front, side and rear tests.
IIHS finds huge benefits of electronic stability control in reducing serious crashes, accelerating introduction of this feature ahead of federal requirements.
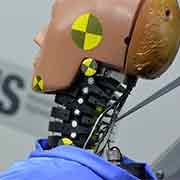
A dynamic test simulating a rear impact is added to the Institute's head restraint evaluations. The test uses a new kind of dummy specifically designed to measure neck injury potential in rear crashes.
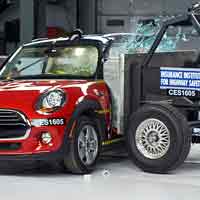
IIHS launches crash tests to rate crashworthiness in side impacts. Automakers respond by improving vehicle designs to provide better protection in side impacts.
Years of IIHS research on teen drivers pay off when the nation's first three-stage graduated licensing law goes into effect in Florida.
IIHS rates head restraints for their potential to protect people's necks in rear-end crashes. Automakers respond with designs that reduce neck injury risk.
IIHS launches offset crash testing to rate frontal crashworthiness. Automakers respond by improving vehicle designs to provide better occupant protection in frontal crashes.
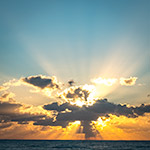
IIHS reveals that daylight saving time reduces crash deaths, a finding that contributes to the subsequent designation of more weeks clock-forward.
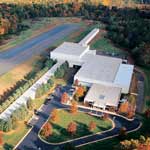
IIHS opens the Vehicle Research Center (VRC) in Ruckersville, Virginia.
Two 1989 Chrysler LeBarons collide head-on in rural Virginia. Both drivers walk away with minor injuries. The crash, believed to be the first of its kind involving two airbag-equipped vehicles, vindicates IIHS and other safety advocates who lobbied for decades for an airbag requirement, which had just been enacted.
IIHS publishes the first consumer information that compares death rates among drivers by vehicle make and model.
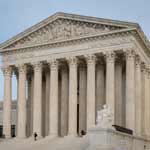
The Supreme Court rules in favor of insurers' efforts to get airbags in cars.
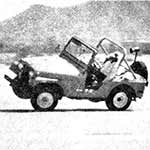
IIHS makes its first appearance on primetime television in "60 Minutes" segment on Jeep rollover dangers.
.jpg)
IIHS is first to document the hazards to pedestrians of allowing motorists to turn right at red lights. This leads policymakers in New York City and elsewhere to resist or limit the practice of allowing right turns on red.
IIHS tests demonstrate the tendency of the Jeep CJ to roll over, prompting the government to require rollover warnings on some vehicles.
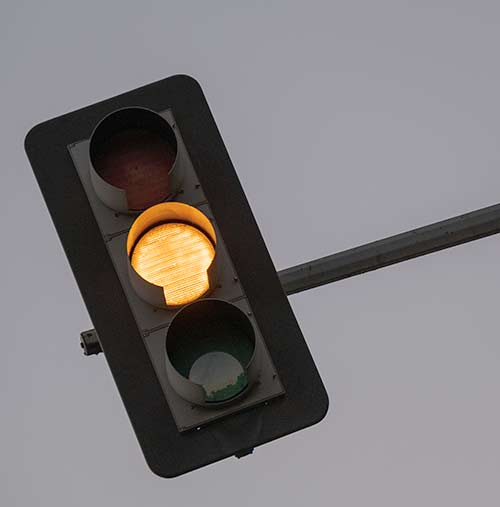
IIHS research on signal timing leads traffic engineers to lengthen yellow light intervals.
IIHS crash tests demonstrate airbag effectiveness in frontal crashes. Highlights are shown before a U.S. congressional committee.
IIHS develops the injury severity score to help medical personnel assess the threat to life of injuries to multiple body parts.
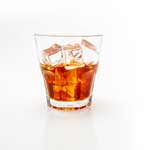
IIHS evaluates the consequences of lowering the legal minimum age for purchasing alcohol. Findings provide the scientific basis for enacting 21 minimum age laws in all states.
IIHS crash tests demonstrate that car fuel system designs allow ruptures, gas leaks and fires in rear crashes. This leads to new federal rules to reduce leaks.
The Highway Loss Data Institute (HLDI) is organized as an affiliate of IIHS to collect, analyze and publish insurance loss information on most car, SUV, pickup truck and motorcycle models on U.S. roads.
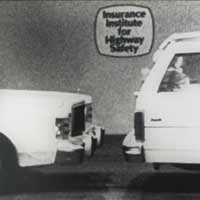
IIHS launches bumper tests, which lead to the first federal bumper standard.
IIHS becomes a scientific research and communications organization after the Board of Governors votes to change its mission.
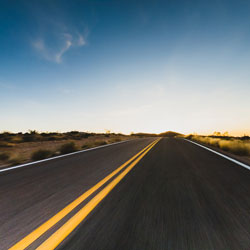
Three insurance industry groups representing more than 500 auto insurers establish IIHS to funnel support to academic and other organizations in the field of highway safety.